Our Researchers and Developers Share their CLC Design Journey in Two Webinars
The CHEERS CLC project is pleased to invite you to two webinars:
1) Wednesday January 12, 2022, 09:30-10:45 CET
2) Wednesday January 26, 2022, 09:30-10:45 CET
You can register here.
The two webinars will highlight respectively
1) the FEED study of its 3MWth demonstration facility, including key work on one of its unique operational features, and
2) development and testing of the oxygen carriers that functions as the ‘blood’ of the energy conversion. As a bonus, in the first webinar, CHEERS will share its results on the wider commercialization potential of full-scale Chemical Looping Combustion (CLC) facilities.
The ambition of the CHEERS project is to achieve quantum improvement in CO2 capture in industry to provide sustainable, secure, and affordable energy. This will be achieved by testing and verifying a 2nd generation CLC technology, first at laboratory and pilot scale and then in a 3MWth demonstration facility that is designed and constructed within the CHEERS project.
The detailed programmes for each webinar are shown below.
1) January 12, 2022 9:30-10:45 (Central European Time):
CLC development: FEED of 3 MWth demonstration plant and industrialization studies
This activity has been led by TotalEnergies, in close collaboration with IFPEN, Tsinghua University and Dongfang Boiler Company.
- Introduction & Presentation of the CHEERS Project
- FEED achievements for the 3MWth demonstration facility
- Industrialization of CLC: case studies
- Conclusions & perspectives
- Q&A
2) January 26, 2022 9:30-10:45 (Central European Time):
CLC development: Oxygen carriers for the 3MWth demonstration plant and future development
This activity has been led by SINTEF, in close collaboration with IFPEN and Tsinghua University.
- Introduction to the CHEERS project and the oxygen carrier work
- Pre-screening of important parameters for Oxygen Carrier under CLC conditions
- Multiscale screening and selection of Oxygen Carriers for the demo CLC facility
- Oxygen carrier testing in a 150 kW CLC unit with solid fuels
- Upscaling the production and fluidised bed testing of a perovskite oxygen carrier
- Conclusions & perspectives
- Q&A
Please feel free to forward this invitation to people in your network.
CHEERS research reports now available for downloading
The CHEERS project is approaching its next major milestone: The start of procuring and building its 3MWth Chemical Looping Combustion (CLC) demonstration facility in China.
The path to this milestone includes a comprehensive set of R&D activities from small-scale reactivity measurements in the laboratory to pilot plant testing, advanced numerical modelling, and flow testing and measurement on a 1:2 scale copy of the planned 3MWth demo facility. Our researchers have documented this work in detail for the benefit of not just CLC developers, but the greater community of technologists working to bring new, improved low-emissions solutions to market.
This is already being facilitated in a number of ways. To compliment these, the CHEERS project has now made available its completed research reports for downloading from the project website. See the ‘Results’ tab on the front page of the website. Some of the research reports are confidential. In this case, only the front page and the publicly available abstract are downloadable.
There is also a pdf file (also downloadable) containing a screen shot of the front page of externally published technical articles from the CHEERS project (i.e. peer-reviewed journal papers or conference proceedings). These can be found on the ‘Cross-Work Package Publications’ tab under ‘Results’.
Recording from our WP2 webinar on July 1, 2021
In case you missed it, or want to revisit the webinar held by WP2 on July 1, 2021, simply follow the link to the recording on our Youtube channel.
Webinar Invitation: Thursday July 1, 09:30-10:45 CET
On behalf of the CHEERS CLC project, Bellona is pleased to invite you to a webinar highlighting the main results from the Work Package 2 ‘Development and Design Studies’. This activity has been led by IFP Energies nouvelles (IFPEN).
This webinar will summarize the research results on the following themes:
· The dual Sino-European CLC design
· 1.5 MW CLC cold flow model design and operation
· Pre-FEED of the 3 MW CHEERS demonstration unit
The ambition of the CHEERS project is to improve the efficacy of CO2 capture in industry, and help ensuring sustainable, secure, and affordable energy. This will be achieved by testing and verifying a 2nd generation chemical-looping technology, first at laboratory scale (150kWth), then developing into a 3MWth system prototype for demonstration in an operational environment.
Please register here.
The CHEERS CLC project has received funding from the European Union’s Horizon 2020 research and innovation program under grant agreement No 764697. The project is also co-funded by the Chinese Ministry of Science and Technology (MOST).
For more information about the CHEERS CLC project, please visit our website
Please feel free to forward this invitation to people in your network.
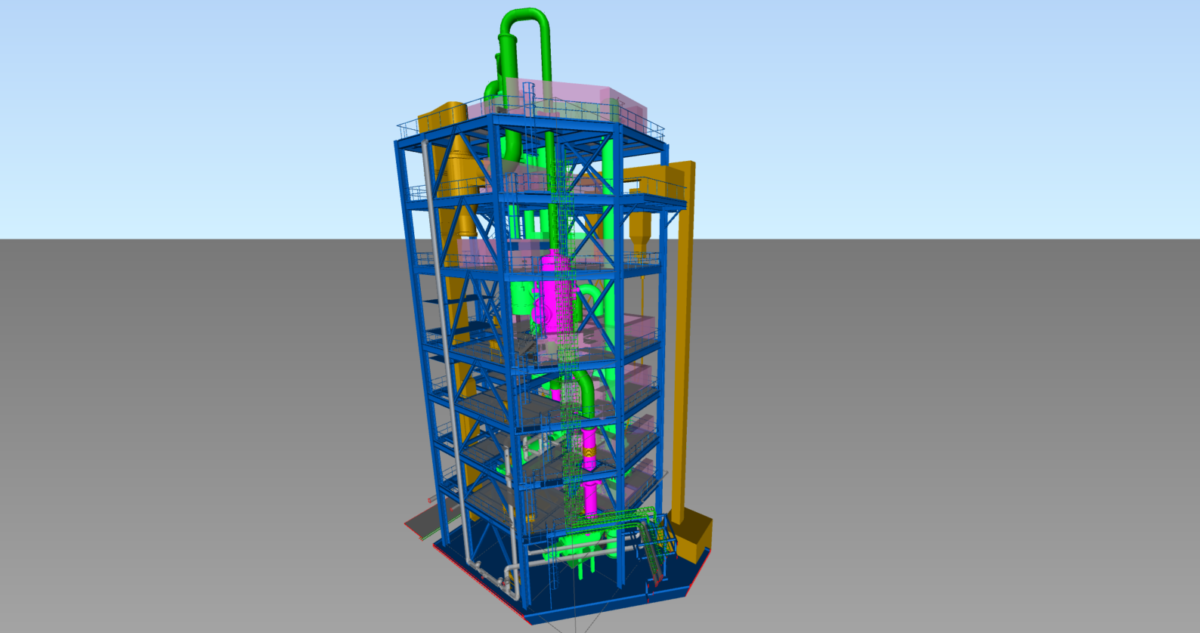
A 3-D engineering rendering of the planned demonstration plant
The CHEERS project launches next phase of industrial scale plant design
Carbon Capture and Storage (CCS) is a key technology to achieve greenhouse gas emission reduction targets and mitigate global warming. CO2 capture is the building block of CCS with considerable impact on the downstream transportation and storage stages.
Chemical looping combustion (CLC) is an innovative combustion technology with inherent CO2 separation. A metal oxide is used to transfer oxygen from the air reactor to the fuel reactor, where fuel is burned without direct contact with air. The resulting CO2 from the combustion part of the process is not diluted with nitrogen from the air, hence, no additional CO2 separation step is required. This is the main feature of the CLC process, which permits inherent CO2 separation with a high degree of energy efficiency improvement and competitive capture cost.
Captured CO2 must satisfy specifications depending on its form of transport and final destination, which may be storage or utilisation. This means that, due to downstream requirements, treatment and conditioning are critical steps in the CO2 capture process.
Various contaminants may be present in the captured stream, such as NOx and SOx, depending on the type and quality of the fuel. Fuels such as natural gas and some biomass feedstocks need little post treatment while heavy fuels, such as petcoke, need NOx and SOx removal units. These technologies are currently deployed at large scale in industrial applications. However, CO2 captured in a CLC plant has some differences compared to conventional flue gasses, such as absence of free N2, lack of or low O2 content and high steam concentration. This makes the flue gas from a CLC plant lower in volume but higher in concentration of contaminants, which results in some specific challenges to be overcome.
TOTAL has launched a development and engineering feasibility study together with HAMON on the CO2 treatment topic. HAMON is a technology provider on flue gas treatment with extensive experience on industries such as power, refining and petrochemicals. This study is focussed on the treatment of CO2 captured from a petcoke-fired CLC plant. Regarding the typical content of this fuel, a complete flue gas treatment scheme is needed including dust particle removal, DeNOx and DeSOx. This will be further completed by drying and compression steps to deliver a CO2 that is compliant with specifications for CO2-EOR usage.
CHEERS project aims at demonstration of CLC technology at 3 MWth scale including feasibility and techno-economic studies for preparation of industrial demonstration. This study permits evaluation of the next CLC development phase, which will be an industrial demonstration unit at a capacity of 30 – 60 MWth. The aim is that success at this stage will result in wide industrial deployment of the CLC technology to produce steam for industrial applications or electrical power with zero or negative CO2 emission and improved energy efficiency. The CHEERS consortium includes Bellona, Dongfang Boiler Group Co. Ltd (DBC), IFP Energies nouvelles (IFPEN), SINTEF Energy Research, SINTEF Industry, TOTAL, Tsinghua University, Silesian University and Zhejiang University.
The CHEERS project is financed partially by the EU’s Horizon 2020 Research and Innovation Programme and the Chinese Ministry of Science and Technology, with financial and industrial support from project partners.
The CHEERS team adds a new peer-reviewed publication to its growing list
The CHEERS project has achieved several research objectives in its quest to design, build and operate what will be the world’s largest demonstration CLC facility.
One of its areas of research has focused on understanding how the particles of fuel and oxygen carriers evolve as they chemically react, change size and density as they pass through the various chambers of the complete CLC system.
The CHEERS team is proud to announce publication of research results in the peer-reviewed journal Combustion and Flame, where the drag force acting on a fully reacting fuel particle is studied and explained in great detail.
This is essential knowledge for an optimal system design, which involves finding the right balance between flow rates, reactor height and diameter, as well as a long list of operating parameters and modes.
One step closer to industrializing a new carbon-free energy production technology
The front-end engineering design (FEED) phase of the Chinese-European Emission-Reducing Solutions (CHEERS) project has now started – a major milestone in this project. When finished, it will be the world’s largest chemical looping combustion (CLC) demonstration plant.
The project is the last step before an industry-wide deployment of CLC technology. CLC generates steam for industrial applications or electrical power, without CO2 emissions thanks to its built-in ability to separate CO2. This means CLC can produce energy with zero carbon content. In addition, It can produce energy with negative carbon content when using feedstocks such as biomass. In this case, CLC enables the indirect capture of CO2 from the atmosphere, and the reduction of greenhouse gas content to the atmosphere.
The demonstration plant – to be built in China – will test the second-generation CLC technology at a capacity of 3MW and will be the largest of its kind using this new fuel-conversion technology in an operational environment.
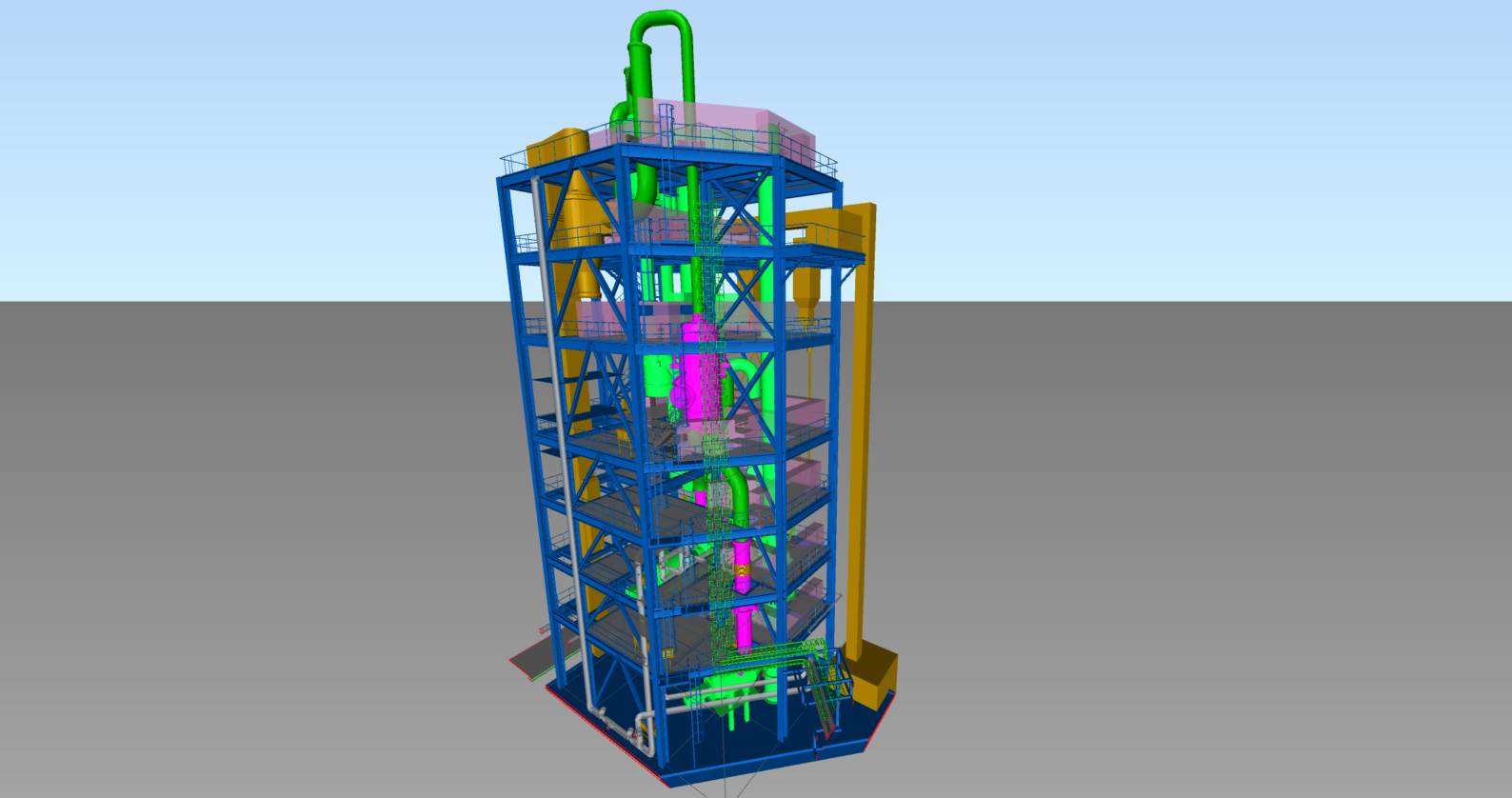
A 3-D engineering rendering of the planned demonstration plant
The ground-breaking concept has the potential to increase the efficiency of CO2 capture significantly, compared to existing carbon capture technologies and can remove up to 96 per cent of combustion-related CO2. The project offers a viable path to retrofit industrial combustion processes and is a major step towards the large-scale decarbonization of the refining, chemical and power industries.
Managed by TOTAL, the FEED was awarded to Worley, who will carry out the services from its Belgium and China offices. Once completed, the FEED results will be handed over to Dongfang Boiler Group Co Ltd, who will manage the detailed engineering, procurement and construction (EPC) of the plant.
The CHEERS project is financed partially by the EU’s Horizon 2020 Research and Innovation Programme and the Chinese Ministry of Science and Technology, with financial and industrial support from TOTAL, Dongfang Boiler Group Co Ltd, and other project partners.
How to design the flow inside a CLC installation
The CHEERS project continues its design and verification work based on the cold flow rig described in a previous post. In this newly produced video of the cold flow rig, more detail and description are provided on the subsystems and components involved.
A very important intermediate step is to build a visualization rig that looks very much like a working CLC plant, but does not use fuel. Instead, it circulates the particles used to transfer oxygen to the fuel in a nitrogen-free environment.
The cold flow rig (sometimes called a cold flow mock-up) was designed, built and installed by our CHEERS partners in Europe and China. This video highlights the special design details implemented on the cold flow rig for European design specifications.
If you are interested in the technical details behind this, then you can read our CHEERS researchers recently submitted article to the peer-reviewed journal Energy&Fuels. This article has been accepted for publication after final formatting for the printed version of the journal.
But if you would simply like to watch the new video with more complete description of the cold flow rig in action, here it comes.
Special thanks goes to our CHEERS project partner IFP Energies nouvelles for producing and editing this new video.
Chemical Looping Combustion: how it works in a new video
The global warming challenge is one of the greatest innovation opportunities going forward. One strategy is to re-invent combustion from scratch to promote more efficient CO2 capture. A very promising such solution is Chemical Looping Combustion (CLC).
The Cheers project is developing Chemical Looping Combustion (CLC) to the next level. CLC is an energy production technology leveraging inherent, built-in, CO2 capture. This reduces the need for investment in dedicated CO2 separation from low-concentration flue gases. It also reduces operational costs because it uses less energy in its inherent CO2 separation process.
Designing a full-scale CLC plant is still a work in progress. The current fleet of CLC test rigs are made and used for basic research and development. These are now ready to be scaled up to dimensions suitable for commercial application.
The CHEERS project has produced the design basis of a 3 MWth demonstration CLC facility with systems that will allow researchers to understand how to make it even better in the next version. This design basis is now being converted to a Front End Engineering and Design (FEED) by a world-renowned engineering contractor. This will be announced in a post coming soon.
The animation below shows how the system works, and what makes CLC a great candidate for re-inventing combustion.
CHEERS acknowledges generous support from the European Union’s Horizon 2020 research and innovation programme under grant agreement No 764697 and the China MOST program.
CHEERS launches new Youtube channel with new video of the scaled cold flow model
CHEERS releases new video from the demonstration laboratory showing the inner workings and flows throughout the CLC installation
The CHEERS project maintains a Youtube channel for its own videos and associated videos that support its basic motivation and objectives. Due to technical reasons, we have moved to a new Youtube channel, which you can find here (subscribe to keep updated). The highest resolution versions of the CHEERS videos will be available there. Lower resolution versions of the same videos will be viewable on the CHEERS web page.
In addition, we are pleased to include a new video produced by our Chinese partner Tsinghua University. In this video, we have a direct view from their research laboratory. The video shows the scaled, cold flow model the CHEERS project has designed and constructed. This cold flow model is built with see-through components that allow direct visualization of the movement of the solid particles in the two reactor towers, the separation units and transfer pipes. The solid particles in the cold model represent the oxygen carrier particles that are circulated in an actual CLC installation. The function of the oxygen carrier particles is to achieve a nitrogen-free atmosphere for combustion, without the need for a separate oxygen production system. This saves significant investment and operation costs, particularly related to CO2 separation.
The cold flow model is essential for validating numerical models that represent the full-scale demonstration plant currently being designed. The results from the cold flow model allow identifying ways to improve the overall performance of the system.