Public Seminar Presentation – Chemical Looping Combustion Design
The presentation lead by Patrice Font, leader of work package 2 and 5 of the CHEERS project and researcher at IFPEN, as well as Professor Zhenshan Li, work package 6 person in charge from Tsinghua University, covered the design considerations under both the European and Chinese partners. Work on chemical looping combustion was investigated by both Chinese and European partners resulting in two different and innovative configurations to evaluate the technology. Testing both these configurations would allow for two different approaches to achieving CLC to be tested.
The common alignment across the different configurations is the use of solid feedstock. The European configuration focuses on petcoke while the Chinese configuration looks at lignite. The difference between the two rather being in terms of the application of CLC technology. The European configuration looks to be applied in a refinery; the Chinese configuration on the other hand, looks at emissions reduction in power generation. The functioning of the plant is still based on solid circulation and hence both configurations are evaluated within the same demo unit despite having the circulation flow slightly altered.
The presentation went through the different valves that govern the core functioning, which allow for solid circulation through the different parts of the unit. Such solid circulation requires pneumatic valves as compared to conventional mechanical valves. There are three main L-valves which control: the oxygen carrier flowrate to the fuel reactor, oxygen carrier recycling around the air reactor and the movement of oxygen carrier from carbon stripper to the air reactor. The European design considers an integrated carbon stripper alongside the fuel reactor whereas the Chinese design realises the two as separate units. The fuel reactor uses a fluidised bed design allowing for longer conversion time for the solid feed to convert to gaseous products.
On the road to a 4 MWth demo unit, a continuous pilot model on the kW scale and a MW scale mockup was developed by IFPEN. Through such process developments, many patents were filed along the way such as the methodology of separation of oxygen carrier and unburnt feedstock. A 1.5 MW cold flow model was developed at DBC which aimed to study crucial parameters such as fuel reactors hydrodynamics, solid circulation between air and fuel reactor, transport of oxygen carrier in air reactor and carbon stripper efficiency. This was crucial in demonstrating the stability of the design in a wide range of operating conditions for both configurations.
The designs proposed by the partners were tested and validated to be realized in the demo unit. The path to the two innovative approaches resulted in a variety of outputs, patents being one such example. For more information on the design of the CLC units and the configurations, do not hesitate to reach out.
Public Seminar Presentation – CHEERS primary test results
Nicloas Vin, R&D engineer at IFPEN presented the primary test results on the CHEERS project based on the demo unit outputs as of the seminar date. The presentation touched on the timeframe from January of 2022, where the construction of the demo unit started. Aside from the rapid construction over 11 months to erect the 44-meter-high demo unit, it was done so with no accident or incident. This holds true even through the operation of the demo unit as well as repair works that it has undergone since the first start-up of the plant on 6th of June 2023.
The oxygen carrier, Ilmenite, required pre-oxidation to ensure agglomeration is avoided. Agglomeration may occur mainly for reduced oxygen carrier particles in dead zones of the demo unit. Confirmed by experiments in a small-scale muffle furnace, pre-oxidation at 800 degrees Celsius avoids agglomeration, and also positively impacting oxygen carrier circulation. 75 tons of ilmenite was pre-oxidised in the fuel reactor.
The circulation of the oxygen carrier is crucial and complex. As a solid consisting of fine particles, controlling its flow rate across the different parts of the demo unit requires pneumatic valves realized by the L-valve. The three valves in the demo unit (X101, X102 and X103) control the oxygen carrier flow from air reactor to fuel reactor and reverse. The presentation highlighted the solid flow rates in the valves function of temperature and pressure.
The presentation also touched upon a challenge encountered with the manhole refractory. The fuel reactor reached significant temperatures at which some slugging solid regime occurred, with large build up of air bubbles in the start-up phase, resulting in the refractory manhole protection to fall down in the reactor. This was solved by improving the tightening of the refractory manhole by providing reinforcement via 4 melded metal supports.
The demo unit thus far has achieved the first validation of the CLC technology via L-valve functioning. Significant data acquisition of the working of the demo unit thus far sets the team up for the next challenges. Looking ahead, the team loops to complete solid circulation and L-valve calibration at 800 to 900 degrees, validation of heat losses for autothermal CLC as well as testing CLC at the 2-4 MW scale. The teams working on the demo unit, both European and Chinese partners are confident and excited to move forward with the next steps for the demo unit.
For further information on the primary results from the CHEERS demo unit feel free to reach out.
Public Seminar Presentation – Integrated assessment for industrial scale-up of CHEERS
Vincent Gouraud from TotalEnergies, leader of work package 4 along with Patrice Font from IFPEN, leader of work package 2 and 5 presented on the techno-economic assessment (TEA) of an industrial scale CLC unit, the design cases relevant for such a scale and finally to benchmark the CLC technology with references considering the full value chain.
Addressing the design cases relevant for industrial scale required modelling the fuel reactor at that scale. To do so, the strategy employed looked at batch unit kinetic studies which were then validated by IFPEN’s 10 kW CLC unit. Understanding the hydrodynamics with the fuel reactor was a necessary step in upgrading to an industrial scale. The demo unit in Deyang, China provides the final validation at the 2-4 MW scale. The process simulation of the CLC plant at industrial scale was also done considering the two use cases: power generation case (at a scale of 200 Mwe) and a refinery case (at a scale of 50Mwe).
With a scope from feed preparation to CO2 compression, r the Techno-Economic Assessment (TEA) at industrial scale, highlight the list of required equipment and their cost. . Quotes were obtained from manufacturers on the equipment needed. This TEA is done on the 500 MWth scale with key KPIs being the levelized cost of electricity and the CO2 avoided cost.
The TEA looks at both CLC use cases, refinery and power generation at the respective scales and two reference technologies : CFB circulating fluidised bed and natural gas combined cycle. The resulting 6 combinations are evaluated, and cost estimates were createdConsidering core assumptions to help build the TEA, it confirms that CLC technology is competitive for solid feedstock for both use cases. The levelized cost of electricity is lower for CLC as compared to CFB with amine-based capture and cost of avoided CO2 lower for CLC as well. For comparison with the NGCC case, price sensitivities were introduced to understand what price ranges are favourable for CLC.
The study confirms that CLC is a cost competitive option for reducing emissions in both power generation and refinery cases with solid feedstock. Transport and storage of CO2 costs would impact these costs as a full value chain was evaluated by SINTEF.
For more information, feel free to reach out.
Public Seminar Presentation – Design to pre-FEED and FEED
The Front-End Engineering Design (FEED) is the crucial step before the construction of the demo unit. It covers the technical requirements for the realization of the project. The pre-FEED and FEED studies were carried out from 2018 to 2021. The studies carried out by both the EU and China faced additional challenges apart from the time difference as the COVID pandemic posed significant difficulties in terms of information exchange and collaboration. The presentation of this journey was done by Vincent Gouraud from TotalEnergies, leader of work package 4 and was carried out by Mahdi Yazdanpanah.
The FEED study was successful in considering both European and Chinese configurations. The configurations differ in terms of interaction of the carbon stripper with the rest of the system. Both these configurations were incorporated within the demo unit and can be interchanged. This is increasingly complex considering that the final construction of the demo unit must take into account the separate configurations and their process limitations. 23 design cases were studied, and the controllable parameters were further evaluated. These parameters presented considerable range, for example, the power of the unit can range from 2 to 4 MW thermal, considering thermal input from 66 to 133% of capacity. Considering the fuels for the reduction in the fuel reactor, solid fuels Lignite and Petcoke were considered.
These levels of complexity were not the only challenge, as the unit was a first of its kind in many aspects; L-valves to control solid circulation do not exist at this scale, neither does the specificity of the oxygen carriers changing density along the red-ox cycles. The CLC demo unit requires complex engineering due to solid circulation among many other factors.
Finally DBC premises overcome the challenge of setting up the construction of the 44-meters demo unit between existing buildings. And furthermore, The construction of the demo unit was done in 11 months, a relatively short duration of time.
Despite such a multitude of challenges, the results from the FEED study were significant. Such a study resulted in 235 documents; these documents describe in detail the technical specifications such as process design through to engineering standards but also crucial safety documents such as the HAZID (Hazard identification) HAZOP (Hazard and Operability) and LOPA (Layers of Protection Analysis) studies. The HAZID study analysed 83 cases, identifying 5 potential causes of major accidents and generated 35 key recommendations.
FEED documents produced valuable resources for design and evaluation of industrial scale of the CLC plant, which is useful for further work beyond CHEERS. This highlights the successful intercultural collaboration between the Chinese European partners.
For more information on these topics or a deeper dive, feel free to reach out.
Public Seminar Presentation – Oxygen Carrier Material
Øyvind Langørgen from SINTEF and Lei Liu from Tsinghua University presented at the public seminar of the CHEERS project on the 20th of September at Deyang, China. Covering the work done on the topic of the oxygen carrier material within work package 3, the presentation went through the selection of the oxygen carrier, its subsequent testing and validation.
The oxygen carrier is a crucial part of the chemical looping combustion technology. The oxygen carrier would transfer the oxygen from the air reactor to the fuel reactor for fuel combustion. It must also transfer the heat necessary to sustain the combustion process. These two functions ensure that this type of oxy fuel technology results in a clean stream of CO2 with very low impurities while achieving chemical looping combustion. Oxygen carriers are typically metal oxides, based on metals such as iron (Fe), manganese (Mn), calcium (Ca), or copper (Cu). These carriers can be both natural and synthetic, and to identify the correct choice many tests were conducted; first through lab scale screening tests, then through testing in CLC pilots and finally validation at the pilot scale CLC units.
Properties were prioritized when considering oxygen carriers that would best suit the CLC process. This included the capacity to transfer oxygen, fuel conversion and reaction kinetics, the lifetime of the material, and the availability and cost of the material. One of the initial materials selected was Ilmenite (FeTiO3), multiple sources were tested of this material; from Norway, Vietnam and Mozambique. This naturally occurring material was tested at different heat conditions and the Norwegian sourced (Titania) Ilmenite T2 proved to be the most effective. Despite being and appropriate candidate, initial testing at high temperatures resulted in agglomeration of the material which proved to be a barrier for achieving CLC.
As an alternative, a synthetic material Perovskite – Ca(MnxTiyFez)O3 was tested in the batch fluidized bed unit at IFPEN. The results showed partial deactivation of the material due reaction with sulphur. This alternative be was discarded as the feedstock used in the European configuration, Petcoke, has significant sulphur content.
Turning back to Ilmenite, the reason for agglomeration was evaluated. It was found that the issues lie in the delivery of the material being dry. By pretreating the material, via the addition of steam, it was noticed that agglomeration was avoided. This reduced fuel conversion and oxygen transport capacity but well within the design limits. Tests were then carried out with the material at 15 kW and 150 kW scales with various feedstocks: Petcoke, biomass and a mix of the two, showing positive results.
While the Ilmenite was being evaluated at SINTEF, Tsinghua University tested the synthetic material CMTF Perovskite. The results from 1000 cycles showed no agglomeration and short oxidation time of only 4 seconds. It also had a longer lifetime compared to the ilmenite alternative. With these benefits came a significant difference in cost; nearly 2000 USD/ton of the material whereas Ilmenite was priced well belove half.
Considering these parameters, ilmenite was chosen to be the ideal candidate for the role of oxygen carrier for the CLC process. The work package had managed to validate 3 oxygen carriers in this process. Ilmenite met the criteria for performance, cost, sulphur tolerance and availability among other parameters. 250 tons of ilmenite was shipped from Norway to Deyang, China for the pilot plant for testing of both the European and Chinese configurations.
For more information on the oxygen carrier work done on the CHEERS project, feel free to reach out.
CHEERS project overview – Interview with Nils Haugen, European Project Coordinator
Nils Haugen from SINTEF is the project coordinator of the Chinese European Emissions Reducing Solutions (CHEERS) project. Apart from overall management, Nils oversaw the technical and scientific progress of the project. In this interview, he shared some key insights from his experience with the project over the last six years.
Were there any key milestones in this project that you would like to showcase?
“There have been several. One thing was that we got the cold flow unit up and running and got to test the fluidization. That was a very important validation of our design models.
Then of course it was the Front-End Engineering Design (FEED); finalization of the FEED showing that this [carbon capture with chemical looping combustion] could be done. As a follow up on that, a very important milestone was to actually agree on the cost sharing, which led to the final investment decision. That was a big milestone I would say. Of course, the commissioning was also a big step. Now we have finalized commissioning, and the unit is standing there and is currently in the startup phase.”
How long will the demonstration unit be running for?
“We will do the testing of the pet coke design first. This will probably go on through this year. The project formally ended by the end of September but we will continue some months longer than that to be able to finalize the testing. And then, after the pet coke design testing has been finalized, the lignite testing will start, and I guess it will continue for maybe half year.
I also expect, this will not be within the CHEERS project though, that some of the core partners will continue with other feedstock, for example biomass, or other oxygen carriers.”
How did the findings of the project contribute to the development and improvement of carbon capture processes?
“I think the big step that is being made by CHEERS is that we are building the world’s largest CLC unit, up to 4 MW, to bring the technology closer to commercialization. Another very important thing is that the unit is designed and built based on commercial engineering principles; it’s not set up to be used in a lab.
So, when you look at the demonstration unit as it’s standing now, the first commercial unit will probably look pretty similar when it comes to its main design and height. The main differences will be that for a commercial unit the two reactors will have larger diameters and there will be less measurement ports. I think that is the biggest contribution here; that we are showing that CLC can be utilized on a commercial and industrial scale.
Also, what we have shown in the technoeconomic assessment is that when it comes to solid fuels the CLC technology will be beneficial, certainly over any kind of amine-based capture methods. It looks very good for solid fuels; and CLC is the optimal option for (CO2) capture when it comes to solid fuels.”
How does this technical research contribution fit into the broader climate change mitigation picture?
“I think there are some very important places where the CHEERS technology can really contribute.
For example, if you want to do BECCS (Bioenergy with Carbon Capture and Storage); so, you want to burn biomass, which is a solid fuel and it’s really ideal to have a CLC unit for CO2 capture with biomass.
It also seems that for many kind of wastes, like these pretreated wastes that can be fed into in the unit, it will also be a good option for producing heat and power with inherent CO2 capture. Furthermore, we of course have the same benefit if you look at waste such as pet coke. Finally, it also seems that there could be good potential for gasification or reformation, for example for blue hydrogen production.”
The oxygen carrier choice, is it still beneficial for biomass?
“Yes, if we had been using biomass, Ilmenite would still be okay. But we may actually have chosen a different one because there are some synthetic oxygen carriers that show very good performance. But those that we tested did not tolerate the sulphur levels of pet coke, which is rich in sulphur. But for biomass those kind of synthetic oxygen carriers that we studied in the beginning of the project really seemed to have a huge potential. They are significantly more expensive, but the lifetime will be much longer and there will be less waste to handle.”
How can the technical knowledge accrued in this project be used in research and innovation?
“There are two pathways that I think should be pursued. One is to take the technology of CHEERS and scale it up. This means to build the first commercial unit, which could have a size of around 30-50 megawatts. I think that would be the most important next step.
The other thing is to not upscale, but to show that we can do for example the blue hydrogen or BECCS at the same scale. This means that the same CO2 capture process and knowledge accrued in the project can be used for different applications.”
Has your work identified any research gaps that needs to be addressed?
“One thing is the oxygen carriers. We need to identify which one should be used at large scale. Also, what should be done with them afterwards? Can it be utilized somehow or are they just plain waste?
Another thing is that for upscaling purposes we want to be able to do accurate and reliable numerical simulations, which will allow us to do much cheaper parameter studies. But also very importantly, it is a very harsh environments inside these reactors. This means that it’s very difficult to have measurements probes in there. But if you can do good numerical simulations of these units, it will help a lot when it comes to understanding their inner workings. Identifying these numerical models is something we are already working on.
Another issue where there could be a research gap is utilising waste as a sort of fuel. We will have to do some pre-treatment of the waste, but how much pre-treatment do we need? We want to pre-treat as little as possible because pre-treatment is expensive. But at the same time, we want to be able to actually feed the fuel into the system and then it should be converted in the fuel reactor in an efficient way.
Another topic of interest is that, up to now, the vast majority of all testing with CLC has been done with well-defined homogeneous fuels. So, figuring out how to cut costs would be the next ask. One very beneficial aspect about CLC is that all the pollutants are in the fuel reactor while the heat is typically released in the air reactor. This means that you don’t need any heat exchangers in the fuel reactor where you have the troublesome species from the fuel. Instead, the heat production is in the air reactor, which is clean such that you avoid problems related to fouling and corrosion.”
CHEERS Final Event Announcement
The Chinese European Emissions-Reducing Solutions project is drawing to a close. The six year Sino-European collaboration has brought together multiple project partners with a goal of improving the efficacy of CO2 capture in industry. Funded by the EU Horizon 2020 research and innovation program as well as the Chinese Ministry of Science and Technology, under European Horizon 2020 work programme 2016-2017, 10. ‘Secure, Clean and Efficient Energy’, the CHEERS project brought together a variety of actors: Bellona Europa, DONGFANG Boiler Group, IFPEN, Silesian, SINTEF Energy Research, SINTEF Industry, TotalEnergies, Tsinghua University, Zhejiang University.
The project looked at an alternative to conventional amine based CO2 capture by maturing chemical looping technology which was prior tested and verified on a laboratory scale. CHEERS looked at building a demonstration unit at scale; from 150 kW thermal in laboratories to an operational scale of 3 MW thermal. After a multitude of research outputs and learnings, the finished demo unit in Deyang, China has entered its start-up phase.
A key milestone in verifying operational characteristics of the core technology at scale, CHEERS hosts all the project partners at the inauguration event of the pilot plant in Deyang, China. Our project partners look forward to sharing more information from discussions and results from the 19th – 20nd of September as the project partners convene to take the final steps towards realising much needed research to vital decarbonisation technologies.
Summary of CHEERS Webinar held on 25th of January 2023
CHEERS or Chinese European Emissions Reducing Solutions is an international R&D project, funded partially by the European Union (Horizon 2020- Research and Innovation programme), to demonstrate a second generation carbon capture and storage (CCS) technology at relevant size, taking it up to technology readiness level (TRL) 7. The key deliverable of this project is to design, construct and operate a chemical looping combustion 3MW demo unit and validate with pet coke and lignite feedstock.
The webinar held on the 25th of January 2023, moderated by Ana Serdoner from Bellona Europa, hosted all the actors of the consortium. European partners represented by Sintef, Total Energies, IFP Energies Nouvelles, Bellona and Silesian University of technology, while the Chinese partners were represented by Dongfang Boiler group, Tsinghua University and Zhejiang University. The presentation touched upon various aspects, updating the processes and methodologies undertaken as well as the key technical takeaways from the project.
Scope of Work Packages:
Stephane Bertholin from IFP Energies Nouvelles kicked off the discussion by setting the scope of the work package, highlighting the objectives: provide techno-economic assessment of the industrial Chemical Looping Combustion- Carbon Capture and Storage (CLC-CCS) unit, address different design cases relevant for industrial needs and Benchmark CLC technology including full CCS chain and Life Cycle Analysis (LCA) perspectives.
The work package was split into 3 phases: the first being the modelling of the reactor at industrial scale which was completed over 2018 and 2019. The second being the process simulation carried out over 2019 and 2020. The final phase being the Techno-economic study carried out from the data gathered from process simulation, concluded in 2021.
Reactor modelling:
Nicolas Vin from IFP Energies Nouvelles dove deeper into the strategy of realizing a reactor model. The first model was initially developed from studies available at IFP EN, used to validate operation based on experimental results. Further the model was upgraded to an industrial scale and hydrodynamic models were added. The final step, validation of the demo unit itself, is yet to be done.
The modelling was done using both a batch unit as well as a continuous unit, allowing for the study of parameters such as temperature, CO2 content etc. as well as pet coke and oxygen flowrates. The modelling held up against the experimental results, to which Nicolas Vin notes “it means the physics is well represented [in the model]”.
Process Simulation:
Moving on the process simulation of the industrial scale model Catherine Laroche from IFPEN highlighted the two uses cases that the simulation tested: power generation (200MWe) and refinery (50MWe). “We decided to have two design cases in order to assess the performances of the process at two different scales” says Catherine.
As the CLC reaction with inputs such as pet coke generates a lot of heat, there is significant steam that can be used to generate electricity. Two different reference CCS combustion plants were used to benchmark the CLC plant. The first, a natural gas combined cycle plant, the second a circulated fluidized bed plant, both using standard amine based capture technology. The natural gas plant considered both Mono ethanolamine (MEA) and an advanced solvent Piperazine/2-amino-2-methyl-1-propyl (PZ/AMP) while the second only looked at MEA. The demo reactor unit (3MW) is representative of these two references in size, nearly matching its height, but differing significantly in width.
Elaborating on efficiency, Catharine compared the outputs of a 200MWe power plant with the different benchmarks. The thermal power efficiency of the CLC plant sits between the Circulating Fludised Bed (CFB) and Natural Gas Combined Cycle (NGCC) plants, but the net electric efficiency lagged behind both in the simulation. However, the high capture rate of 97% in the CLC plant results in a CO2 emissions factor of 29 kgCO2/MWhe, significantly lower than both NGCC and CFB plants. The amount of CO2 captured for storage is also higher in CLC and CFB plants compared to NGCC due to the nature of carbon content in pet coke as compared to natural gas. These aspects point to the conclusion that CLC would be the preferred technology when pet coke is used as fuel due to higher net power efficiency, lower specific emissions and higher capture efficiency.
Techno-economic assessment:
Vincent Gourand from Total Energies touched upon the economics of the CLC plant and the full chain through the techno-economic assessment. “To get the best and most accurate techno-economic assessment, we wanted to have the best figure for the CAPEX and OPEX. We selected a few companies to get quotes for different parts of the CLC.”, he says.
Starting with the CO2 flue gas treatment, which constitutes 20% of CAPEX of total plant costs, the technology is oxy combustion which results in very little nitrogen that needs to be separated and is a highly concentrated stream of CO2, making capture easier and cheaper.
Vincent presented several Key Performance Indicators (KPIs) based on the established hypothesis that the plant would consider 2019 prices. The first KPI presented was the levelized cost of electricity, putting the CLC plant at around 100 euros/MWh not considering transport and storage costs. Compared to the reference technologies, this places CLC Levelised cost of energy (LCOE) lower than that of CFB but higher than that of NGCC. By including price sensitivity of natural gas in the NGCC plant (an increase of 50%), the LCOE of the NGCC plant climbs higher than the CLC case.
The second KPI discussed was the cost of avoided CO2 (euro/tco2). For the power generation study, the CLC case fared significantly better compared to CFB reference, with CLC placed at 98.5 euro/tco2 avoided, whereas the CFB case rose to 254 euro/tco2 avoided. NGCC reference technology fared slightly better with and without capture compared to the CLC case. For the refinery study, the results were similar, the only difference being that the costs rose significantly for both CFB and CLC cases (379.5 and 184.8 euro/tco2 respectively). The third KPI presented was the net present value and cost of avoided CO2 in the refinery case. Here, like in the previous case, CLC performs better than CFB case but falls short of the NGCC case significantly.
A couple of sensitivity analyses were introduced as well, for the power generation case, the oxygen carrier sensitivity was evaluated using mineral oxygen carriers (usually cheaper) and synthetic oxygen carriers and the inventory change over specific time periods. The second sensitivity introduced was the capture rate. Decreasing the capture rate (by reducing the efficiency of the carbon stripper) of the CLC plant does not greatly impact the cost of avoided carbon.
Simon Roussanaly from SINTEF touched on more of the economic aspects of both power generation and refinery cases. The sensitivity due to fuel prices was checked, benchmarked against NGCC case. Ranging the 2019 price of gas by 50% on either side and pet coke price by 100% on either side. The matrix so formed shows the diagonal on which it makes more economic sense to opt for CLC over NGCC, requiring significant reductions in pet coke price and increase in natural gas prices. Moving on to the costs associated with the CLC and NGCC cases, the LCOE and Net Present Value (NPV) pointed to higher values for CLC due to larger volumes of CO2 to be captured and transported. This alludes to lower residual emissions for the CLC case.
Considering the full chain of CCS, the costs affect the matrix formed by the fuel price sensitivity. It reduces the available range of fuel cost considerations that allow CLC to be economically more viable than the NGCC case for the power generation case. For the refinery case, the window for CLC to be economically viable shrinks further.
Moving to the conclusions, Simon summarized the caveats, for a solid feedstock such as pet coke, CLC fares far better than CFB with carbon capture for both power and refinery case. NGCC is mostly a better option compared to CLC, especially in the refinery case, with the comparison becoming competitive only due to price sensitivities and reduced distance to storage sites.
Life Cycle Analysis:
Elodie Gaouyat from Total Energies elaborated upon the life cycle analysis of the CLC project. In particular, the evaluation loops to check the environmental performance of chemical looping combustion process to produce electricity in comparison with CFB and NGCC with carbon capture. The LCA takes a cradle to gate approach with the functional unit of 1kWh of electrical power and does not include the use of produced electricity nor the transportation or storage of CO2.
The LCA shows a 43% reduction in GHG emissions in the CLC case compared to the CFB, with 66% if emissions in CLC case due to pet coke. These reductions are proportional to capture rates; higher the capture rate, higher the reductions. Despite high capture rates, CLC still fares worse compared to NGCC. The other environmental impacts place CLC above CFB but in general, NGCC fares the best. Regarding other environmental impacts, CLC still requires increased mineral resources such as CACO3 and water due to use of ammonia.
The webinar concluded with interesting questions raised by participants resulting in engaging conversation with the presenters.
CHEERS demonstration facility construction is advancing rapidly to completion
The CHEERS consortium has designed and developed a 3 MWth demonstration facility for chemical looping combustion (CLC). This work began in 2017 and includes a comprehensive program of laboratory measurements, pilot-scale testing, cold-flow visualization rigs, and detailed simulation modelling on microscopic and macroscopic scales.
The CHEERS industrial partners, Dongfang Boiler Group and TotalEnergies, with close assistance from research partners Tsinghua University, IFPEN and SINTEF, are now well underway to build the facility on-site at the Dongfang Key Laboratory for Clean Combustion and Flue Gas Purification at Deyang, Sichuan Province, China.
The goal is to start testing on the completed facility in Q2 2023. Site preparation of the integrated CLC plant began in Q1 2022. Subsequent construction and assembly have progressed impressively. Most of the internal process equipment, much of which is unique to the CLC design, was completed in July-August.
- The footprint of the CLC system is about 270 square meters, and the highest process unit will be about 42 meters tall.
- The project aims to confirm the designed carbon capture rate of 96%.
- The capabilities of the CLC facility include enhanced system monitoring and data collection to enable a deeper understanding of the system performance. This will be used to improve future designs.
- The design of the CLC demonstration unit includes special adaptations to use at least two different types of solid fuels. As part of the design phase activities, these have been extensively modelled numerically and with an analogue 1/3 scale ‘cold flow’ hydraulic version of the final demonstration unit.
The following photos show some selected snapshots from the construction site and the factory producing the main process units.
The CHEERS project has received funding from the European Union’s Horizon 2020 research and innovation program under grant agreement No 764697. The project is also co-funded from National Key Research and Development Program of China by Chinese Ministry of Science and Technology (MOST) under grant agreement No 2017YFE0112500.
The project has also benefited from the work of the other project partners: Silesian University, Zhejiang University and Bellona.
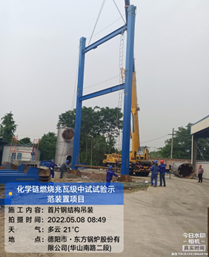
Raising the first steel beems for the support structure May 2022
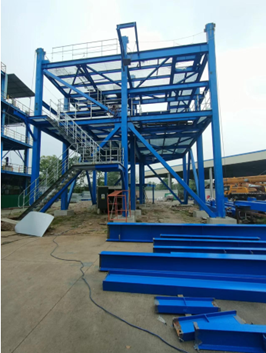
Steel Support Frame June 2022
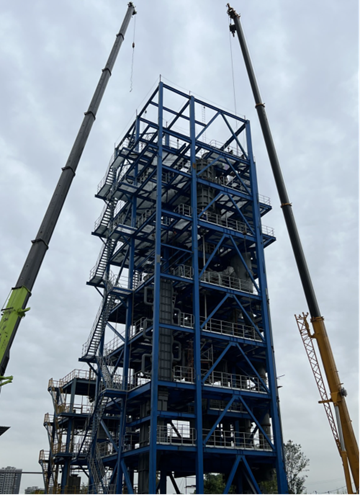
Steel Frame Support Structure in place August 2022
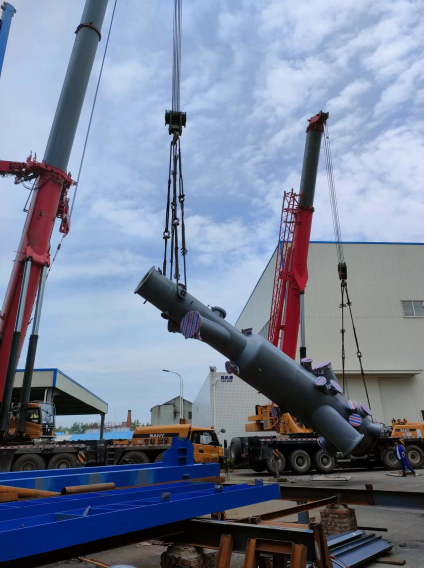
Installing a major process component in the demonstration facility August 2022
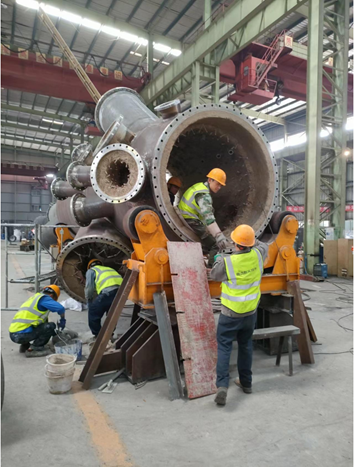
Manufacturing the main process units for CLC June 2022
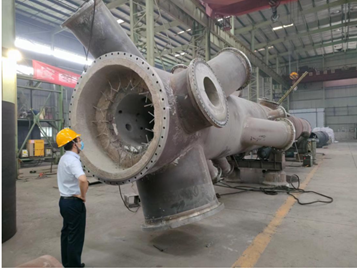
Manufacturing the main process units for CLC June 2022
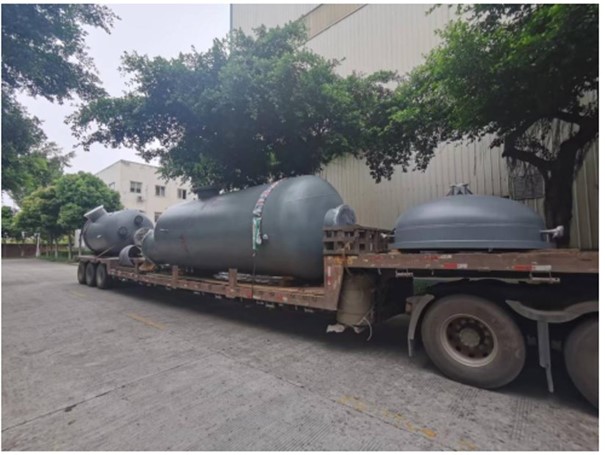
Transport of finished tank units to demonstration facility site June 2022
Building of the Largest Chemical Looping Combustion (CLC) Facility to Drive down the Cost of Carbon Capture
Paris/Deyang City (China), February 2, 2022 – CHEERS, a Sino-European consortium of leading researchers and manufacturers, has announced the construction of the world’s largest demonstration unit for Chemical Looping Combustion (CLC). This new stage will bring the project to a pre-industrial scale and confirm the potential of this key technology in driving down the cost of carbon capture and promoting the decarbonization of industry. Today the project reached a new milestone when TotalEnergies, Dongfang Boiler Group Co. (DBC), Tsinghua University and IFP Energies Nouvelles made the decision to build the 3MWth demonstration unit, with the potential to deliver 4-5 MWth.
Lowering the cost of carbon capture in power generation
CLC is an oxy-combustion technology used to convert biomass and fossil fuels in order to obtain a flow of pure CO2 suitable for low-cost capture. This integrated CO2 capture solution minimizes the use of costly gas separation processes like those retrofitted on existing combustion facilities. CLC generates heat that can be used to produce carbon-neutral electricity and/or steam.
“This unique project paves the way for the decarbonization of industries that currently generate a significant proportion of global carbon emissions. It could open the door to more cost-effective biomass and fossil fuel emission reductions at facilities around the world,” said project leader Dr. Nils Erland L. Haugen from SINTEF.
“Decarbonizing energy production is a major challenge. The TotalEnergies R&D teams carried out the research and design phases that enabled the CHEERS project partners to take this step and green-light the construction of a pre-industrial unit to validate the technical, economic and environmental performance of the CLC technology,” said Philip Llewellyn, Carbon Capture, Utilization and Storage Program Manager, TotalEnergies.
Developing technology from concept to reality
The investment decision marks the transition from the research and design phases to the engineering and construction phases, led by DBC at their technology development site in Deyang, near Chengdu in China.
The test campaign, planned for 2023, will bring the new concept to near-commercial maturity (Technology Readiness Level TRL 7) and form the basis for further upscaling and commercial project development.
The initial investment in the Deyang demonstration unit will total almost €10 million, in addition to the €10 million already invested in the research and development activities.
“The CLC process is the result of 13 years of research conducted by IFPEN and TotalEnergies on a laboratory scale and on a 10 KW pilot unit in IFPEN’s laboratories. The building of a demonstrator on a pre-industrial scale is therefore a very important step that will allow us to verify the performance of this CO2 capture technology and to prepare its implementation in power plants and biomass plants in particular,” said Florence Delprat-Jannaud, CO2 Coordinator, IFPEN.
**********************************
Facts and figures
- The planned CLC facility will convert a flow of solid fuels of about 4 MW measured in thermal energy content. The footprint of the facility will be about 270 square meters, and the highest process units will be about 40 meters tall.
- The project aims at a carbon capture rate of 96%.
- The capabilities of the CLC facility include enhanced system monitoring and data collection to enable a complete understanding of the system performance. This will be used to improve future designs.
- The CLC facility design includes special adaptations to use at least two different types of solid fuels.
The CHEERS project has received funding from the European Union’s Horizon 2020 research and innovation programme under grant agreement No 764697. The project is also co-funded from National Key Research and Development Program of China by Chinese Ministry of Science and Technology (MOST) under grant agreement No 2017YFE0112500.